Darrell McCulloch: Why I make lugs
Australian frame builder Darrell McCulloch has been making his own lugs for many years and by now is renowned as one of the finest lug workers in the world. He explains how, and why, he found himself in this position.
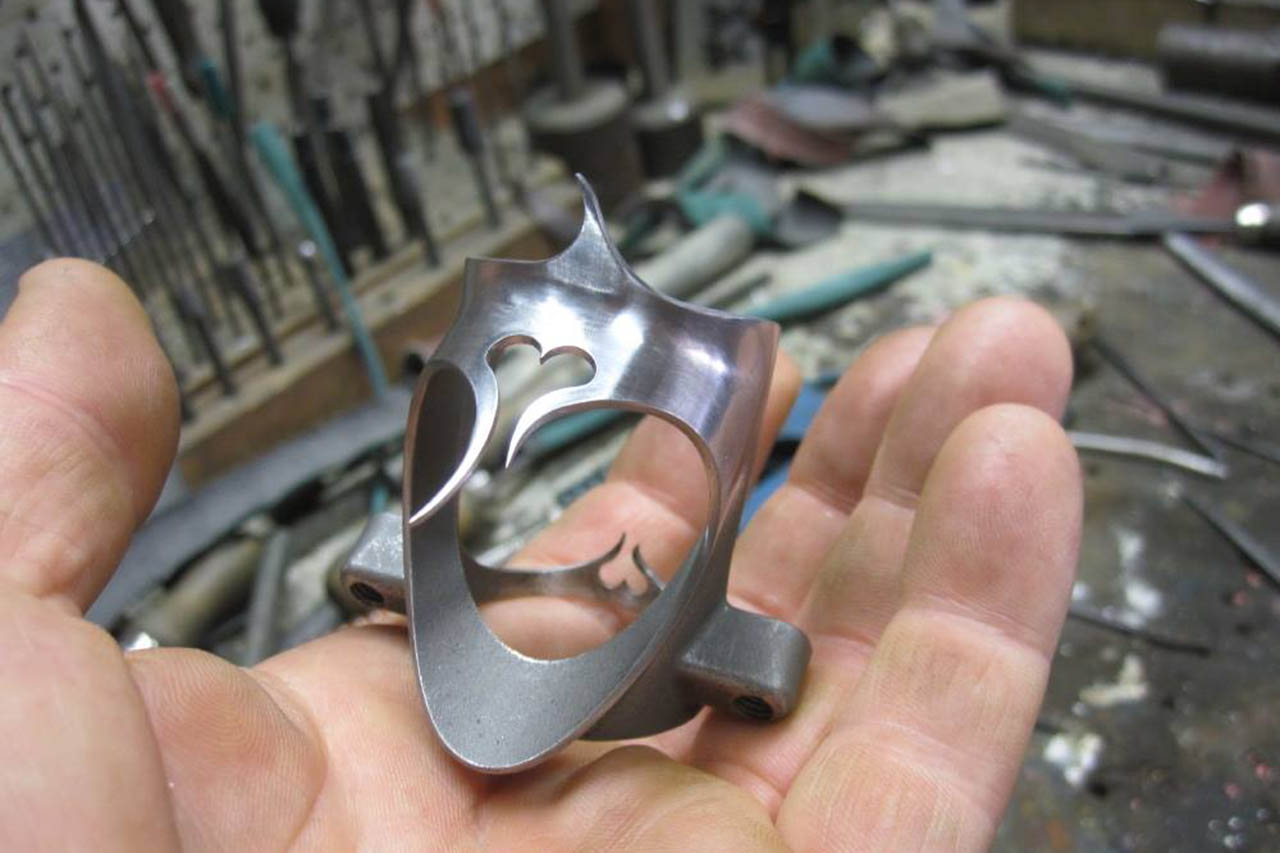
My chosen method of bicycle frame making is lugged steel frame construction. It is my desire to create rider-cherished frames using a blend of the best time-honoured and proven frame construction methods, along with the best of contemporary design. I have an incessant urge to better what I did last week at the bench, to keep progressing my skills, processes, knowledge and to improve the function of the steel hand-made frames that I build. One result of all this is that for several years, by now, I have designed and produced many new, improved lugs and fittings for lugged frame construction.
As you can imagine, designing and producing new castings demands many hours of toil, and other resources too, so you might wonder why I would create new lug designs and parts for steel frames while there is still a substantial variety of these parts from the '80s and early '90s available? There are a few reasons.
Often the historical cast lugs, as they exist now, are constrained by the limitations of their era. Lugged steel frame construction has evolved in many ways, and lugs and parts should fit the requirements of 21st century technology. That might sound harsh, but it's not meant that way and it might help if I explain a little about my background.
I started work at Hoffy Cycles in Australia in 1979, in its back-of-the-workshop frame making area, when I was a keen 16 year old bike racer. I lived the Cycling life: work, train, sleep, race on the weekend, and back to work on Monday - all to earn enough $ to fund racing the following weekend.
At that time, quality hand made frame construction was undergoing change with the introduction of Italian-made investment cast lugs and other frame parts that were replacing press-formed frame fittings. I remember studying these new pieces: lugs, bottom bracket shells and fork crowns with a deep intensity and fascination, often pausing to ponder if it would ever be possible that one day I could make frames with frame parts that I designed and produced?
The new parts were certainly an improvement, but when using them in frames I sometimes struggled with basic design issues. Issues such as bottom bracket shells that had chainstay ports at the wrong angles, lugs with tube fits that were near impossible, and some parts with so much bulk they looked like they belonged on agricultural farm machinery! I tried to comprehend how these issues might have occurred. Perhaps there was a lack of the right experience, or lack of communication, maybe a disconnect somewhere between the designer, the mould maker, and the frame builder? Whatever, I realized that ultimately I would have to be responsible for my own casting designs.
Plans for my own lugs had to wait for several years because of the racing and mechanic work, and making bicycle frames after hours. Then came my years working as an Australian national team mechanic in Europe. Meanwhile the large corporations pushed into the high end of the market, producing bikes for the nth percentile human. The independent frame making caper went from the ubiquitous lugged steel construction of the 1980s to today’s much smaller niche bespoke frame scene.
The 21st Century arrived and I settled down into full-time frame making. Finally I had time to start exploring the path of designing and producing frame parts.
These parts would not be designed to exploit a perceived demand in the frame builder’s market, primarily they were to meet the needs of my own Llewellyn workshop production.
While I found my lugs served my own purposes very well, I was still looking at recouping the considerable investment of time and tooling costs. It seemed reasonable that if the lugs worked for me they would work for other builders too, so I offered these new parts to other builders through the European agent Ceeway, and in North America through Nova Cycles Supply.
So far the reception has been more than I had hoped for, and it is rewarding to see builders around the world using these parts I have designed and produced, many built into award-winnings frames.
It’s toil, but it’s nice.
The Llewellyn casting chronology
2004 Llewellyn Stem Lugs – First handle bar stem lug set for 1” and 1 ⅛” forks and 31.8mm handlebars.
2004 Crescendo XL Compact – World’s first road frame specific sloping top tube lug set for XL (DOS) tubes.
2005 Little Fella Gear boss – Stainless Steel investment cast threaded M5 down tube gear cable boss. (31.8mm and 35mm DT)
2006 Manorina Compact –road frame specific sloping top tube lug set for OS tubes.
2006 Llewellyn Dropouts – Front and rear investment cast dropouts with and without twin M5 threaded eyelets
2009 Llewellyn Track Dropouts – Track dropouts with enough material for placing on larger stays with stainless steel wheel bike facets.
2009 Custodian – Level top tube lug set for OS tubes.
2009 Cadenzia – Level top tube lug set for XL (DOS) tubes, designed in partnership with Dario Pegoretti.
2010 Limpets – Stainless gear and brake cable bosses.
2013 Randonneur rack brake mount rack bosses.
2016 Nipper Seat binder boss for external butted seat tubes
2017 Cadenzia -XLH-04 – optional seat lug for socket fitting seat stays.
2017 Crescendo -XLS-04 – optional seat lug for socket fitting seat stays.
All photos in this article courtesy of Llewellyn Custom Bicycles.