Timothy Rowan of Rowan Frameworks Interview - Part 2
Part 2 of Anna Schwinn's interview with British framebuilder Timothy Rowan of Rowan Frameworks.
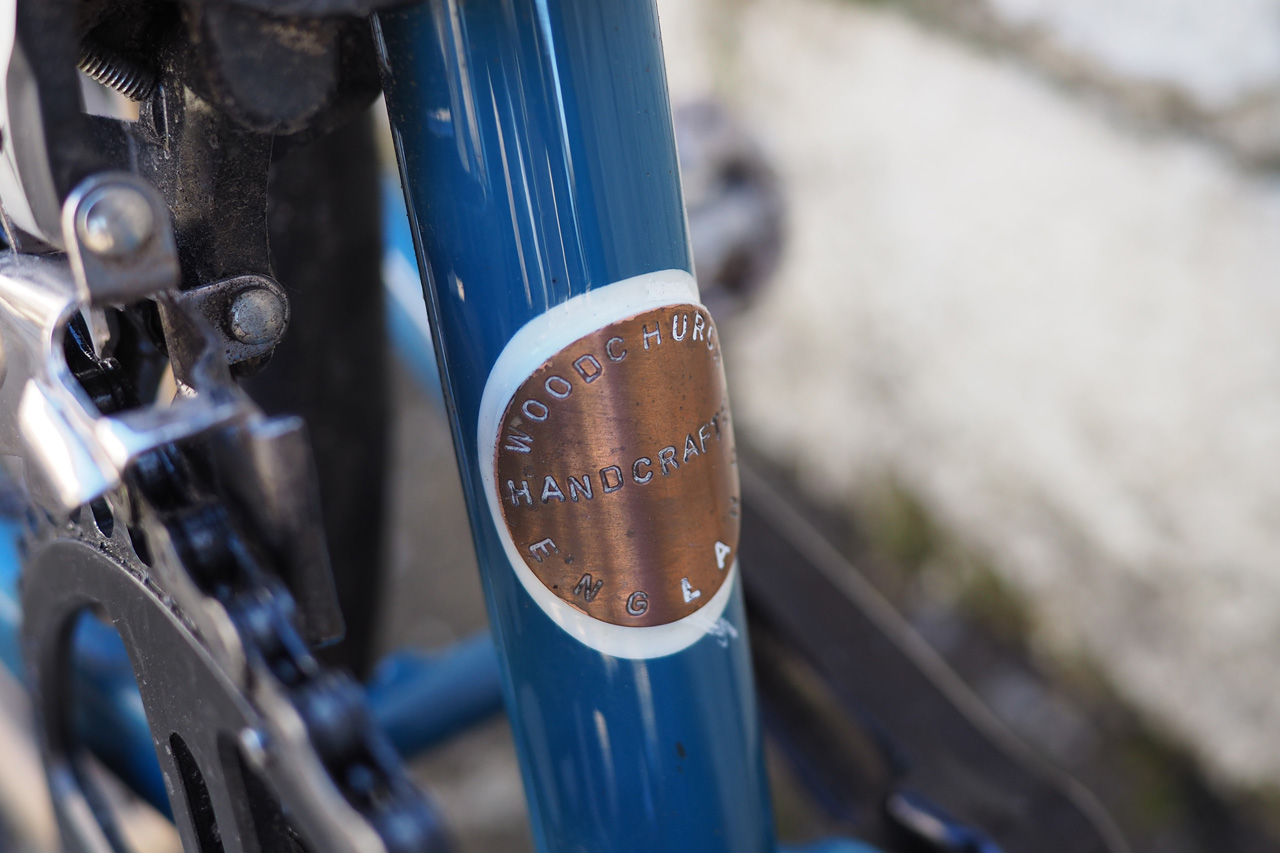
AS You did this practice period, and went back to The Bicycle Academy and built your first bike.
TR Went back and understood roughly what I wanted to do which, at that point, I thought, “Right, I’m going to try to put a few different processes into this bike.” That was this cream cyclocross bike. I’ve stolen some parts for that. It always happens. One bike which is fine, and everything else is… nothing is really built up. So that was lugged with a fillet brazed bottom bracket. I quite like that look. I quite like just not being too ashamed of putting one thing next to another to see if it works.
AS This style of seat stay caps…
TR So that was, if I rewind now to the point where I made the jump, there was a builder I followed, Ezra Caldwell. He made really beautiful, incredibly simple bicycles, beautifully executed. When people talk about “kit bicycles,” I suppose that’s what this is. Standard lugged, cleaned up, but it’s in the way you do it, the way you choose to put things together.
AS Those are his caps?
TR Yeah, so he would do a way of capping them where it was really quite blunt. You see this, quite a lot of it’s a much more shallow angle. Sometimes we call them top eyes if it's a plug, but blunt, scalloped, your finger just sort of sits in there. Very tactile.
All photos: Anna Schwinn
AS Did you do the stem at TBA also?
TR No, I did that here. I came back and did that.
AS I can’t imagine that splitting the class is typical. It seems like a really smart way of doing it.
YR Yeah, let’s really separate it into two different things and then just practice the hell out of it.
AS I’m thinking, man, you must have really annoyed the rest of the kids in the class. You come in after doing all this practice work. The other kids have had only a few days…
TR But there’s so much to learn. I see this bike as a thousand mistakes. It is what it is, that’s my first bike. It looks better with the seat and cranks. It works. It’s really fun to ride. It feels spritely. Once I finished it, the whole thing was nickel plated first for durability, then copper plated on top, then painted on top of that.
It was always the intention to have these exposed areas. You can see how we’re getting this gnarly verdigris. I guess at some point, this will all go green and furry, and I love that, I love that idea. It’s masked around here, I have an incredible painter, but he’s masked it just a tiny bit over so you have this bright line.
The idea behind the copper is that- when I had these as show bikes they were like 50% there because they weren’t being ridden, weren’t covered in mud or actually being used. I was thinking about how you can make a bicycle that actually gets better with age, because if you scratch a beautiful pristine bike or dent it before you give it to a customer, then that’s ridiculous. That’s not something you can do. But to have exposed customer or an element that will age. Like this fabric bar tape that you see wear, or raw denim, or old leather boots.
AS Where age improves it.
TR Yeah, but how would it work for a bike. That’s the goal. Bikes that age and get better with you.
AS You only have have two machines in this shop, a lathe and a drill press. But otherwise, nothing.
TR Yeah, just the hand files. The half round file, that’s the majority of the work, really. It does the job.
AS How many bikes have you made at this point?
TR One, two, three… seven… eight?
AS How long have you had this shop?
TR About a year. Too long.
AS That’s not bad starting out. Tell me about this bike you have in process on your stand. Tell me about this process.
TR This one particularly, a guy came to me and said it would be fun to have a kind of [Integrated Seat Post]- he wanted an ISP style. I thought, okay, if we do that, then we have to put a reinforcement ring. If I do that, then I might as well do some flourishes. If I do that I might as well do like a bilaminate head tube. So often, one design decision just keeps going. So I ended up with three internal routing down the downtube. That goes around to a stainless piece.
I hadn’t really seen this in bilaminate or lugs, these blunt straight lines like a knight’s helmet. So bluntness just translated and kept going. I thought, if it’s going to sit like that, it should be deliberately sharp and blunt at the same time. These caps are straight and flat. It is quite fun when you allow yourself to be part of the process. It isn’t fully designed until you’re actually using your hands and things are kind of moving.
AS The blunt transition between the chainstays and the dropouts is really cool. Because you take so many liberties when you’re finishing a joint like that, you really only realize that you’re taking those liberties when you have something exposed like that. In order for that style of transition to really work, everything has just got to be so deliberate. Can’t be off center. It has to be perfect.
TR Yeah, and it’s so easy to almost braze this part in and if you then make a decision when you’re sitting there with the file, it’s kind of too late. There are just so many considerations with that. Oftentimes, someone will blend it around the chainstay, but obviously when you’ve already curved this part of the dropout, at one point do you taper that out and then back into flat- you can’t have a full curve then taper straight out into flat.
AS You have to choose your lines.
TR Yeah. As soon as you kind of go off, it can really send you sort of squirrelly. Like if you start to think, okay, I’ll blunt that one and I’ll curve that one to there… if it’s not working…
AS Would you like to talk about your klunker? It is kind of counter to everything else you have going on here. You have these flawless aggressively detailed and finished bikes. And then you have this!
TR There’s details! Like this: a tiny bit of brass.
AS You made a little knob for your fork tip because you don’t have a spring in your brake!
TR [These brakes] are really hard to get. They arrived with four right hand springs. Goddamn it. So I turned this tiny little brass thing on a lathe just to hold the elastic bands in place. It’s good.
AS This was with Andrew from the Bicycle Academy. The plan was: get a bunch of framebuilders with limited time and funding to build klunkers.
TR Had to be cheap. Had to be kind of hack bike, just thrown together. It was fun. I built the bars first.
AS Why..? Why solid brass handles?
TR Why not? I don’t know, just feel it. It feels like a caveman bike.
AS So what number bike was this?
TR Seven maybe? So fun. The dropouts had to be hack as well. Literally just a piece of steel in the vise and hacked at it with an angle grinder- I allowed myself a power tool.
AS So these are handmade dropouts, huh?
TR Took me two or three hours. Whole thing took me three or four days. It was so fun, it was really liberating as well. Creating new shore lines, big attention to detail.
AS And turning brass knobs for your elastic bands for your brakes. And the axe! The axe is great. Did that come in handy? Did you use it?
TR Yeah.
AS For the fire jumping. Obviously. Why did I ask such a dumb question? Your workshop is really put together. You’ve got that cool sort of repurposed wood as slatboard. If you have your mechanic area over here with the flat board so you don’t lose anything.
TR All these are solid oak from the woodman down the road. You go to him and he seems like the most scary, hostile woodsman, but as soon as you start to talk wood... I was there for three, maybe four hours just discussing it. The gnarliness of it. Because if you’re going to stand there for the majority of your life-
AS - you might as well have something to look at. Wow, so this is a year old shop.
TR I don’t know what it’s going to look like in ten years.
AS Yeah, but it’s really well thought out. Did you look at other people’s shops to understand?
TR Yeah, yes of course.
AS Whose shops did you look at?
TR Everyone.
AS Were you just flipping through instagram and websites and books?
TR Yeah. Understanding how things are laid out and what tools do I actually need. Obviously, you can never have too many tools, but if I had a hacksaw and a 10in and a 12in half round file, you’re pretty much- and then your oxyacetylene rig, it’s funny. That was funny. I’m building things up, gradually, in terms of my measuring tools, finding creative ways of using things and repeat all ways of measuring accuracy in things is a fun process. Not trusting things as well. I got this Anvil Type 4 jig- it’s ridiculous, not overkill, but absolutely perfect. And the first thing I do is I just measure the whole thing, measure the shit out of it. It was like okay, my tools can’t measure closer.
AS What were you using for a fixture before that?
TR This is what I had for my first build.
AS You go this right off the bat. Wow, you just went in fully committed. You said you might move into machines eventually?
TR I don’t know, it’s just- the funny thing is people talk about the efficiency of using machines. I understand it if you’re really in production because the amount of time you’ll save mitering an entire bicycle might be half a day. But the time you spend sending emails to the customers and understanding the bicycles and going through that process- some of those orders I have 30 or 40 emails in obsessively understanding of what we’re going to build. That’s where time can really be saved. I think it’s easy to kid yourself and say I need to expand quickly. But there are people who have been building 30-40 years with a hand file.
AS Winston Vaz was saying that. I can do it faster, I’ve been doing this forever. I don’t need specially tooling for special tubing. I can use whatever tubing I want.
What genres are you hoping to get into?
TR Man, if I could do everything like [the klunker], that’d be great.
AS So how do you design your bikes?
TR BikeCAD. The ability to just change something quickly- I want to do everything myself unless someone can do something better than me. My painter is excellent. He does a really lovely job. He’s equally crazy. Before the show he didn’t sleep for a couple of weeks and gets just really obsessed.
People seem to be coming to me with gravel, touring, and adventure bikes. I want to make bikes for the weekend. Chuck a few things in the front and ride off and go camping. Stuff you can strap things to. Very practical. I built a bike for Jacob. That was a fast disc tourer, a race oriented geometry, but he could handle it.
AS What is your process with geometry?
TR My bike fits are through Tony Corke who’s just incredible- as I said, if there is someone else who can do it better. And his wealth of experience is fantastic. He throws away the plumb line and he doesn’t measure your knee angle, but he gets you working and using your muscles. Just tries to understand how that is feeling in your body. He makes tiny adjustments, micro adjustments, and understands how that is translating into rider dynamics. He’s really really good. I think you can shoehorn 90% of people into bike fits using specific algorithms and formulas or bullet points, but there’s always going to be like 10% or 5% of people who are like “this isn’t working for me.”
AS You said you were, in addition to bike crafting, you were into- so that’s a sewing machine. What’s going on with that? You’re engaged in other crafts. Were you into sewing before bike building? Or were you just making stuff in your personal life and being frustrated with the world?
TR Yeah. Actually, that’s what pushed me over the edge. If you can get yourself really annoyed, you’re more likely to do it.
AS Wow, so that was it. You’ve only been doing this for a year. You have three little girls at home. You’ve managed to find this stunning workshop in a part of the world where it’s difficult find a workshop. It seems like a pretty good program.
TR Yeah, I hope so. For a lot of people it would be really easy to keep their jobs and doing it hobby.
AS But you, you just jumped right off the edge of the cliff.
TR Yeah. I really did